Lean Construction: Management Practices That Have Moved from the Factory to the Jobsite
Lean Construction, intended to maximize value and minimize waste, is not simply an add-on to business-as-usual, but a paradigm-shifting concept.
Although the term "Lean Construction" is often bandied about by those who want to discuss its merits in detail or by those who wish to dismiss it quickly as irrelevant, in truth very few construction professionals understand its potential and power. This latest in a series of articles (followingProductivity and Cost Control) will define and dissect Lean Construction and its impact on a jobsite.

“Lean Construction,” as defined by theLean Construction Institute (LCI), is a “management-based approach to project delivery... [that can]... maximize value and minimize waste.” How can a construction manager or general contracting firm really apply this definition in everyday practice? One of the quickest ways to do this is by becoming educated. Good teaching and good practice require a good student. The first step in beginning to understand the breadth of this exciting, emerging delivery process is to join an organization focusing on Lean Construction practices. In addition to the Lean Construction Institute, the Associated General Contractors of America has anonline forumdevoted to expanding and discussing the Lean Construction process.
Furthermore, it is imperative that a firm understand the roots of the Lean Construction process: industrial and systems engineering. Catch phrases like “QA/QC,” “Six Sigma”, and “Lean Construction” all have their pedigrees in early 20th century process engineering. Starting at Bell Laboratories in the 1920s, Walter A. Shewhart began quantizing statistical methods to apply a metric to process. This innovative but ingenious practice has morphed into what we now call Lean Practices today. Starting on the manufacturing floor and moving into the jobsite, the important essence of defect and variance removal can be applied to a construction project. Numerous educational books address statistical quality control (SQC), total quality control (TQC), and total quality management (TQM). Taking a truly academic approach, one outstanding book that can be applied to construction is “Managing for Quality and Performance Excellence” by James R. Evans and William M. Lindsay. This is a great jumping-off point that gives both a high-level and in-depth understanding of the history and uses of lean processes.
Lastly, a value-added approach to understanding Lean Construction as a viable business model is to attend a Lean Construction conference.The International Group for Lean Construction (IGLC)holds a three-day conference in San Diego on July 18–20, 2012, focusing on workshops, research, and coursework. Guest speakers include both industrial professionals and academic professors.
Lean Construction, like BIM, integrated project delivery (IPD), and cost control, has an integral place in the construction process. However, more importantly than that, these streamlined process controls are not going away. As America begins to extricate itself from the grip of The Great Recession, the savvy firms that want to compete will remember that progress for this competitive industry only moves in one direction – forward – while processes, dollars, and time continue to grow leaner.
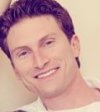
Mark Kowalczyk
Mark Kowalczyk works for Hathaway Dinwiddie Construction Company and is currently building a $70M biopharmaceutical HQ for Agensys in Santa Monica, CA. He has a masters in construction engineering and management from USC, and also teaches undergraduates in construction management.